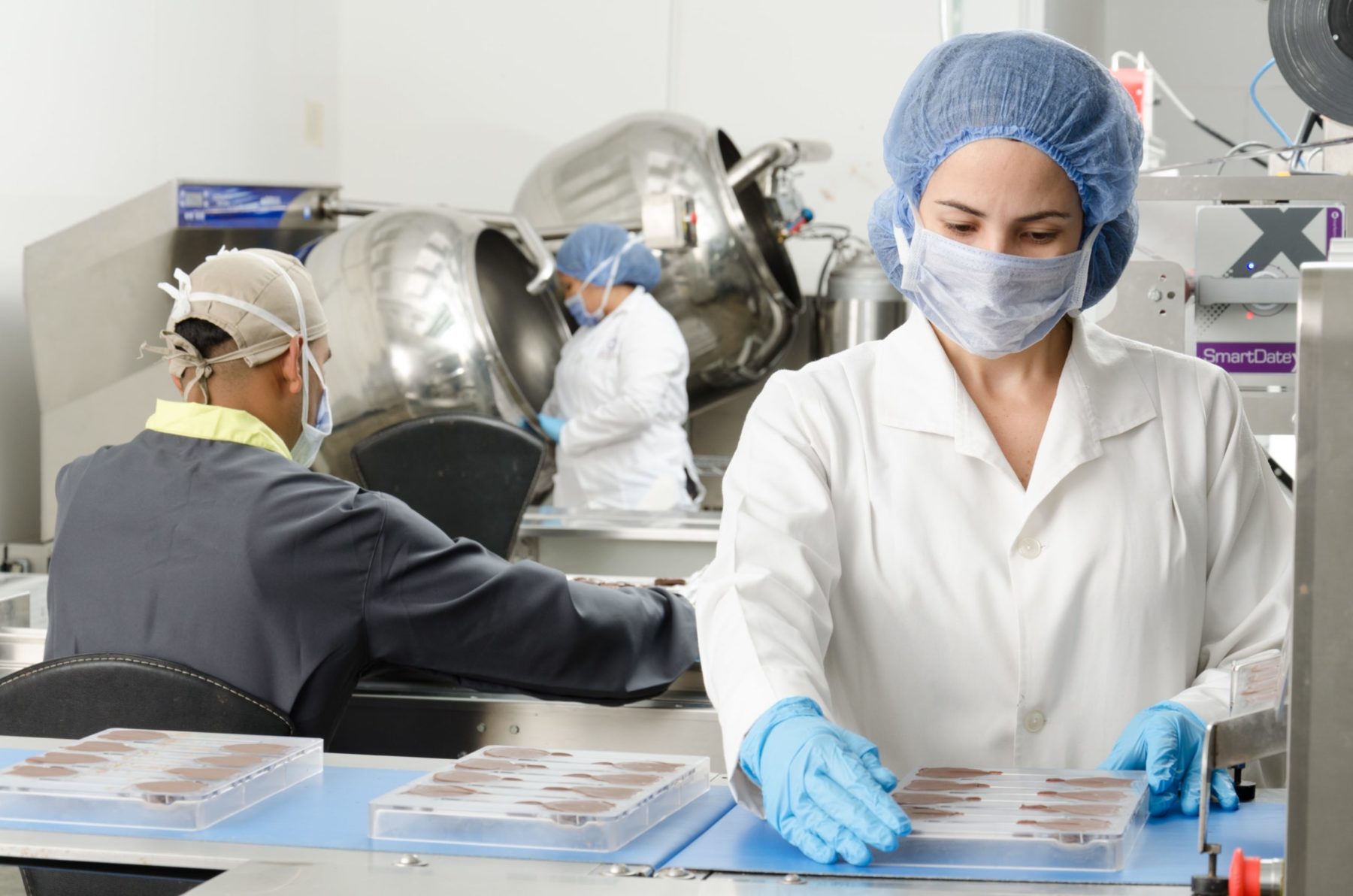
Food Safety
The Economic Argument for NGS in the Food Safety Lab
Working in a cost center can be challenging at best and soul-sucking at worst. Many food safety professionals have heard their departments referred to as “drains on profits” or simply as “overhead,” and they’ve felt pressure to reduce costs.
But how? There are only so many levers one can pull. Technology vendors have limits on their price negotiations. Companies still need to pay their lab workers. Plus, there are the costs associated with inventory holding times and diverted or destroyed products.
That’s where next-generation sequencing (NGS) can help. By abandoning legacy technologies like PCR and embracing NGS, food safety labs can transform a cost center into a margin contributor and make positive contributions to the bottom line.
Reduce Costs Associated with False Positives
False negatives grab headlines in the press, but false positives are thorns in the sides of any food manufacturer. When a false positive presents itself, companies have to absorb the costs associated with destroyed, diverted, or reworked products. On top of that, federal agencies require equipment examinations, intensified sampling and testing, reviews of procedures and records, and so on.
All this adds up. In 2007, an incorrect association of tomatoes with Salmonella Saintpaul resulted in a nationwide recall that cost growers and packers more than $30 million.
Needless to say, life would be easier for food manufacturers if they could reduce the number of false positives they encounter. That’s a key benefit of NGS. With greater than 99.9% accuracy, NGS platforms dramatically reduce the rates of false positives and all the costs associated with them.
Reduce Inventory Holding Time
Gaining control of inventory is a pain point for companies in the food and beverage industry. Margins are slim, products are often perishable, and cross-contamination can happen if foods are stored in proximity.
That’s why many executives are eager to ship product quickly.
In the infamous case of the Peanut Corporation of America (PCA) from 2008 and 2009, Stewart Parnell allegedly instructed his employees to “just ship it” when they wanted to know what to do when test results came back positive for Salmonella. The result? A four-year investigation by the U.S. government and $144 million in economic losses.
Of course, the PCA example is an extreme case. When following standard protocols, companies typically hold inventory while they await confirmation and serotyping results after positive tests.
What are the daily inventory holding costs for your company? Take that number and multiply it by the turnaround time for your confirmatory tests. If you consider that confirmation can take up to five days, that adds up quickly. Granted, waiting for confirmation is certainly cheaper than the $144 million that PCA faced or the millions in hard costs and brand destruction a company faces if a recall is required. Nevertheless, holding costs are unwanted expenses.
An NGS platform can help alleviate this pain point. Within roughly 24 hours, from sample to result, NGS-based testing can deliver not just speciation results, but serotyping results on positives as well. This condenses the amount of time needed to receive serotype information significantly.
What is more, since NGS platforms have greater than 99.9% accuracy, not only will the number of false positives be reduced; some companies may view NGS-based positive results deterministically. In other words, they will take a positive result from an NGS platform as a true positive. Instead of waiting for confirmation, they will immediately divert, rework, or destroy their products, thereby cutting their losses.
Reduce Hands-On Labor
Lab managers are always searching for ways to eliminate bottlenecks and save on labor costs. “Walk-away” time is of the utmost importance because it gives employees the opportunity to move beyond hands-on labor to accomplish other research and development activities.
That’s where NGS platforms enter the scene. A good NGS platform, purpose-built for food safety, will automate some of the menial tasks through robotic liquid handlers, which are geared for high-throughput testing. Because of these innovations in automation, employees do not need to intervene during key stages of the testing process and have more time to work on new projects.
That said, NGS technology’s contribution to the reduction of hands-on labor is not simply a question of automation. NGS platforms make an operational contribution, as well, because they are the ultimate consolidators of technology. Right now, speciation and serotyping are performed separately, requiring additional labor for both. With NGS platforms, however, companies can perform speciation and serotyping at the same time, thus eliminating costly, labor-intensive steps.
Just think of the strategic initiatives that you can undertake if you free up employees!
Want to Learn More?
Contact us. We’d love to give you more insight into the ROI of NGS for routine pathogen testing.